Discover What is Porosity in Welding and Its Impact on Structural Stability
Discover What is Porosity in Welding and Its Impact on Structural Stability
Blog Article
Porosity in Welding: Identifying Common Issues and Implementing Ideal Practices for Avoidance
Porosity in welding is a pervasive issue that typically goes undetected up until it creates substantial troubles with the integrity of welds. This usual defect can jeopardize the stamina and toughness of welded frameworks, positioning security threats and resulting in expensive rework. By recognizing the origin creates of porosity and applying efficient prevention approaches, welders can dramatically improve the quality and dependability of their welds. In this conversation, we will check out the crucial aspects adding to porosity development, analyze its harmful results on weld efficiency, and review the very best methods that can be embraced to minimize porosity event in welding procedures.
Common Sources Of Porosity

Another constant perpetrator behind porosity is the presence of pollutants externally of the base steel, such as oil, grease, or corrosion. When these impurities are not properly eliminated before welding, they can evaporate and come to be trapped in the weld, triggering defects. Moreover, utilizing unclean or wet filler materials can present pollutants into the weld, adding to porosity issues. To alleviate these usual reasons of porosity, complete cleaning of base metals, correct shielding gas choice, and adherence to ideal welding criteria are crucial methods in achieving top notch, porosity-free welds.
Effect of Porosity on Weld High Quality

The presence of porosity in welding can significantly endanger the structural stability and mechanical residential properties of welded joints. Porosity creates gaps within the weld metal, deteriorating its general strength and load-bearing capacity. These gaps act as anxiety concentration points, making the weld a lot more prone to fracturing and failure under applied loads. Furthermore, porosity can decrease the weld's resistance to rust and other ecological aspects, additionally decreasing its long life and efficiency.
Among the key repercussions of porosity is a decrease in the weld's ductility and toughness. Welds with high porosity degrees often tend to display lower influence toughness and decreased ability to flaw plastically prior to fracturing. This can be especially concerning in applications where the bonded elements are subjected to vibrant or cyclic loading problems. Additionally, porosity can impede the weld's capacity to successfully transmit pressures, resulting in premature weld you can check here failing and possible safety threats in essential frameworks.
Ideal Practices for Porosity Avoidance
To enhance the structural integrity and quality of bonded joints, what details actions can be applied to decrease the event of porosity throughout the welding procedure? Utilizing the right welding method for the specific material being welded, such as changing the welding angle and weapon placement, can further avoid porosity. Routine examination of welds and prompt remediation of any issues recognized throughout the welding procedure are important methods to stop porosity and create top quality welds.
Value of Correct Welding Methods
Carrying out appropriate welding methods is critical in making certain the structural stability and high quality of welded joints, building on the foundation of efficient porosity prevention procedures. Welding strategies straight influence the total toughness and durability of the bonded framework. One crucial element of correct welding methods is keeping the proper warmth input. Too much heat can bring about boosted porosity because of the entrapment of gases in the weld pool. Alternatively, insufficient heat may cause insufficient fusion, producing potential powerlessness in the joint. In addition, utilizing the suitable welding parameters, such as voltage, present, and take a trip speed, is important for accomplishing audio welds with very little porosity.
Furthermore, the selection of welding procedure, whether it be MIG, TIG, or stick welding, should align with the details needs of the job to make certain optimal results. Correct cleaning and preparation of these details the base steel, as well as choosing the right filler product, are likewise essential parts of proficient welding methods. By sticking to these ideal practices, welders can minimize the danger of porosity development and produce top notch, structurally sound welds.
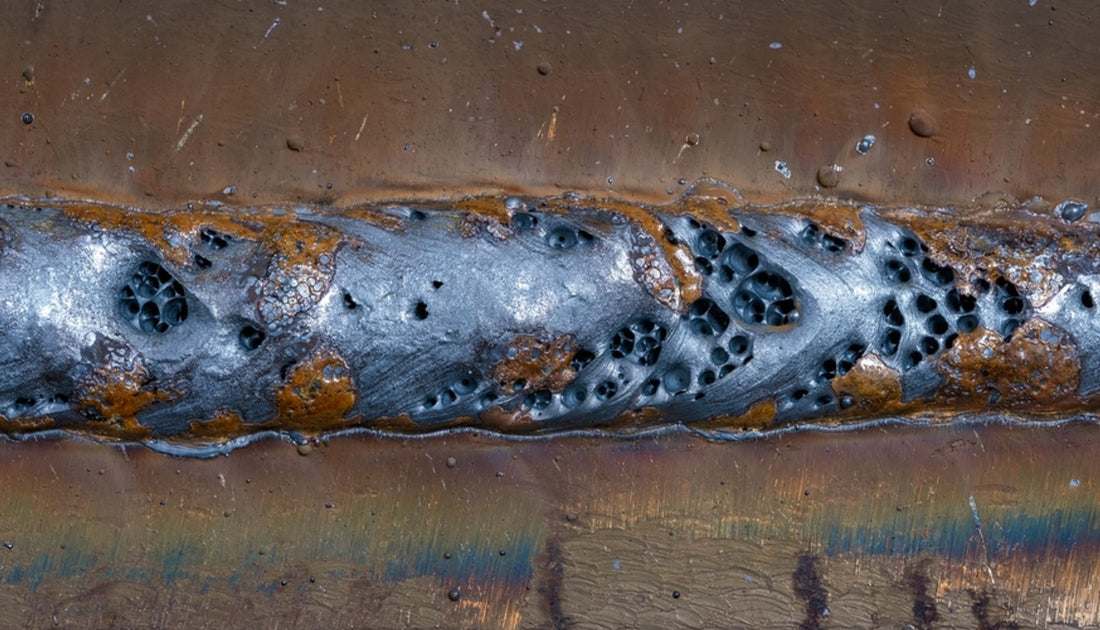
Examining and Quality Control Procedures
Quality assurance procedures play a crucial function in verifying the integrity and integrity of welded joints. Examining procedures are crucial to find and prevent porosity in welding, guaranteeing the stamina and longevity of the end product. Non-destructive testing approaches such as ultrasonic my sources screening, radiographic testing, and visual evaluation are generally employed to recognize prospective issues like porosity. These methods enable for the analysis of weld high quality without jeopardizing the stability of the joint. What is Porosity.
Post-weld assessments, on the various other hand, examine the last weld for any issues, including porosity, and confirm that it satisfies defined standards. Implementing an extensive top quality control strategy that consists of complete testing treatments and assessments is extremely important to lowering porosity issues and ensuring the total quality of welded joints.
Conclusion
In final thought, porosity in welding can be a common concern that influences the high quality of welds. By recognizing the typical causes of porosity and applying finest methods for prevention, such as appropriate welding strategies and testing steps, welders can make certain excellent quality and trustworthy welds. It is vital to prioritize avoidance techniques to reduce the event of porosity and preserve the integrity of welded frameworks.
Report this page